Professor Dr. Joseph Davidovits is a recognized world expert on ancient cements and concretes. Much of the following material is taken from his website: http://www.geopolymer.org. Dr. Davidovits is involved in a great deal of cutting edge research into how the ancients made and used cement. His research is focused on ancient ceramics, mortars, cements, concretes, synthetic stone, and building arts representative of ancient civilizations like: pharaonic Egypt, Mesopotamia, Rome empire, precolumbian America, as well as stone age artefacts from Europe and Asia. We thank Dr. Davidovits and the Geopolymer Institute for allowing us to use materials from his research in this article.
Cement mortar and plaster played an important role in Nabataean life. They used this essential technology from their very earliest years in the desert. Without their special knowledge of cement, the Nabataeans would never have conquered the desert, and would never have risen to the status of a civilization.
Other tribes in the deserts of Arabia lived within the limits that nature put on them. They stayed close to sources of water, and ranged their sheep and camels from there. The Nabataeans on the other hand, built water channels and cisterns far out in the desert to collect the scant rainfall and store it for their use.
Without this knowledge of waterproof cement, the Nabataeans would not have become the far ranging merchants of the Middle East, who easily traversed deserts and inhospitable, barren mountains.
How was it that the Nabataeans developed waterproof cement centuries before its use became common in Europe? In this study, we will begin by examining cement in general, and then looking at how cement was developed and used by other civilizations, especially the Romans. The Romans were contemporary to the later part of the Nabataean Empire, and whose historians recorded for us, how the Romans made and used cement. Lastly, we will look at the special properties of Nabataean cement and speculate about how they developed this amazing technology.
Cement in General
Cement and concrete are often thought of as the same thing, however, they are by nature very different. Cement is an ultra-fine gray powder that binds sand and rocks into a mass which is called concrete. Cement is the key ingredient of concrete, but concrete contains other substances like sand and rocks.
Cement has become one of the world’s most widely used building materials. Annual global production of concrete hovers around 5 billion cubic yards, a volume approximated by yearly cement production levels of about 1.25 billion tons. Concrete’s global appeal is not accidental, for this stone-like material is produced from some of the world’s most abundant resources.
It is important to understand the development of cement on a more global basis, in order to see how Nabataean cement relates to the worldwide development of cement technology. Then we can ask the important question, did the Nabataeans learn their technology from others, or did other civilizations learn their technology from the Nabataeans?
Early History and Development of Cement
The Romans are generally credited as being the first concrete engineers, but archaeological evidence says otherwise. Archaeologists have found a type of concrete dating to 6500 B.C., when stone-age Syrians used permanent fire pits for heating and cooking. These fire pits, built from area limestone, showed a primitive form of calcining on the exterior faces of the limestone rocks that lined the fire pits and lead to the accidental discovery of lime as a fundamental building material. The newly discovered technology was widely used in Syria, as central lime-burning kilns were constructed to supply mortar for rubble-wall house construction, concrete floors, and waterproofing cisterns.
Lime, quicklime, and burnt lime are the common names for calcium oxide, CaO, a grayish-white powder. Today over 150 important industrial chemicals requires the use of lime in order to be manufactured.. In fact, only five other raw materials (salt, coal, sulfur, air, and water) are used in greater amounts. Lime is used in glass, cement, brick, and other building materials; as well as in the manufacture of steel, aluminum, and magnesium, poultry feed; and in the processing of cane and sugar beet juices. It is strongly caustic and can severely irritate human skin and mucous membrane. Thus, the discovery of lime as a building material opened the door for many other improvements as well.
In Europe, archaeological evidence for early use of concrete is also found from along the banks of the Danube River in Yugoslavia, where in approximately 5600 B.C. it was used to make floors for huts.
In China, as far back as 3000 BC, there is evidence of a type of cement used in the Gansu Province of northwest China.
The Egyptians used cement as far back as 2500 B.C. Some scholars believe that a cementing material produced from either a lime concrete or burnt gypsum was used in forming the Great Pyramid at Giza. The earliest known illustration (dating to about 1950 B.C.) of concrete being used in Egypt is shown in a mural on a wall in Thebes. Archeologists have long thought that the Egyptians were masters of the stone as stone artifacts (hard stone vessels, statues) made of metamorphic schist, diorite and basalt were produced. These smooth and glossy stone artifacts (between 4.000 and 5.000 years old) bear no trace of tool marks. Some archeologists believe that the ancient Egyptian artists knew how to convert ores and minerals into a mineral binder for producing stone artifacts. They believe that many of the Egyptian statues were not carved from rock, but rather were cast in molds, and are synthetic stone statues.
The first evidence for this comes from a new deciphering of the C-14 Irtysen Stele (dating 2.000 BC, Louvre Museum, Paris). The stele is the autobiography of the sculptor Irtysen who lived under one of the Mentuhotep Pharaohs, 11th. Dynasty. The stele C-14 of the Louvre has been often studied. Yet many of its expressions pertain to the domain of stone technology and have been tentatively translated in the past with terms differing so widely that the translators were obviously not able to understand the described technology. According to sculptor Irtysen, cast man-made stone was a secret knowledge. (Egyptian Made-Made Stone Statues in 2000 B.C.: Deciphering the Irtysen Stele,(Louvre C14 6 pages) Was this material a type of cement?
Some scientists are now proposing that the pyramids were made of poured stone, rather than quarried stone. From a geological point of view, the Giza Plateau is an outcrop of the Middle Eocene Mokkatam Formation. Yet, the outcrop that dips into the wadi, where the quarries are located and also the trench around the Sphinx and the Sphinx body, consist of softer thickly bedded marly nummulite limestone layers with a relative high amount of clay. The amount of water-sensitive parts, expressed as weight percent of stone, is strikingly very high, ranging between 5.5% to 29%. It is obvious that the builders took advantage of the thickly bedded softer limestones. The disaggregated muddy material was ready for geopolymeric reagglomeration. Perhaps the biggest surprise encountered in this study deals with the hieroglyphic verbs for to build, namely khusi (Gardiner’s list A34). The sign khusi represents a man pounding or packing material in a mold. This is one of the oldest Egyptian hieroglyphs. (Construction of the Egyptian Great Pyramids, 2500 B.C., with Agglomerated Stone. Update of the latest Research,: 42 pages)
The Egyptians also used a more common form of concrete. The durability of their concrete is evidenced by the fact that concrete columns built by the Egyptians more than 3600 years ago are still standing.
The Greeks on the other hand were using cement by 600 B.C., when Greek builders discovered a natural pozzolan that developed hydraulic properties when mixed with lime.
It was the Romans, however, who used cement in large amounts, for huge building projects. Early Roman use of cement dates back to around 300 B.C. Since that period, the Romans steadily improved their concrete technology, they also gave it its name. The word “concrete” comes from the Latin ‘concretus’, meaning “grown together” or “compounded”.
Roman concrete structures still stand today. Both the Colosseum (complete in 82 A.D.) and the Pantheon (completed in 128 A.D.) contain large amounts of concrete. The Basilica of Constantine and the foundations of the Forum buildings also were constructed of concrete. Since Roman cement has been so well studied, it will give us a basis for understanding the issues that are important in investigating Nabataean cement.
Roman Cement
Augustus (33 BC - 14 AD) is reputed to have stated, “I found Rome a city of mud bricks, and left her clothed in marble.” Augustus’ reign is called “the principiate” and it marks the juncture of the Roman Republic and the Empire. Marcus Vitruvius Pollio, who served as an engineer with Augustus´ uncle Julius Caesar, wrote a treatise on architecture during the principiate. Vitruvius quoted earlier authors and defined his ideal in architecture and building, though most buildings of the time fail to meet his standards. Vitruvius´ work and modern archaeological discoveries give us a starting place for our search.
From the digging of ancient Roman ruins, one knows that approximately 95% of the concretes and mortars constituting the Roman buildings consist of a very simple lime cement, which hardened slowly through the precipitating action of carbon dioxide CO2, from the atmosphere. This is a very weak material that was used essentially in the making of foundations and in buildings for the populace. Cato was the first Roman to write about making lime and early Roman construction methods about 200 years before Christ. This book is important to define the practice of making lime under quality control measures. Quality lime was important as it was an ingredient of Roman concrete, and without consistent quality lime the structures of Rome would not survive. (E. B. Rehaut, _Cato the Censor on Farmin_g. Octagon Books, Inc., New York, 1966, p. 64. )
For the building of their “ouvrages d’art”, the Roman architects did not hesitate to use more sophisticated and expensive ingredients. Roman cement has been studied in detail. Initially, conventional mineralogical analysis did not provide satisfactory explanation of the hardening mechanism.
Dusty ancient history books taught us that Roman concrete consisted of just three parts: a pasty, hydrate lime; pozzolan ash from a nearby volcano; and a few pieces of fist-sized rock. If these parts were mixed together in the manner of modern concrete and placed in a structure, the result certainly would not pass the test of the ages.
A most unusual Roman structure depicting their technical advancement is the Pantheon, a brick faced building that has withstood the ravages of weathering in near perfect condition, sitting magnificently in the business district of Rome. This building humbles modern engineers not only in its artistic splendor, but also because there are no steel rods to counter the high tensile forces such as we need to hold modern concrete together.
Solving the riddle of ancient concrete requires understanding the chemistry of the cement, and secondly, understanding how the cement was used.
To understand its chemical composition, we must go back in time much before Moses. People of the Middle East made walls for their fortifications and homes by pounding moist clay between forms, often called pise work. To protect the surfaces of the clay from erosion, the ancients discovered that a moist coating of thin, white, burnt limestone would chemically combine with the gases in the air to give a hard protecting shied.
Sometime around 200 BC the Romans started using volcanic, pozzolanic ash in their concrete. This was an immediate improvement as a chemical reaction took place between the chemicals in the wall of volcanic ash (silica and small amounts of alumina and iron oxide) and the layer of lime (calcium hydroxide) applied to the wall. Later they found that mixing a little volcanic ash in a fine powder with the moist lime made a thicker coat, but it also produced a durable product that could be submerged in water- something that the plaster product of wet lime and plain sand could not match.
Examining the atomic structure of these elements explains what is happening. Common plaster is made with wet lime and plain sand. This sand has a crystalline atomic structure whereby the silica is so condensed there are no atom holes in the molecular network to allow the calcium hydroxide molecule from the lime to enter and react. The opposite is true with the wet lime-pozzolan contact. The pozzolan has an amorphous silica atomic structure with many holes in the molecular network. Upon mixing the wet lime with the pozzolan, the calcium hydroxide enters the atomic holes to make a concrete gel that expands, bonding pieces of rock together. The fine powder condition of the pozzolan provides a large surface area to enhance chemical reaction. This same complex chemistry of the ancient concrete is found in modern concrete bonding gel. The pozzolan-wet lime gel gave permanence to the ancient c concrete.
For many modern concrete experts, the Romans were fortunate builders in that they apparently simply used natural pozzolan deposits, which were found to be suitable for producing a hydraulic mortar. Contrary to this pronouncement, our recent linguistical study and new translation of Latin author Vitruvius’ book De Architectura (1st Century B.C.) states that the magnificent quality of Roman concrete resulted from the extensive use of artificial pozzolanic mortars and concretes. Two artificial pozzolans were intensively manufactured: calcined kaolinitic clay, in Latin testa and calcined volcanic stones, in Latin carbunculus
In addition to these artificial reactive ingredients, the Romans used a natural reactive volcanic sand named harena fossicia wrongly translated as pit sand or simply sand by modern authors. The ingredients testa, carbunculus and harena fossicia were intensively used in Roman buildings. These reactive ingredients must not be confused with the traditional pozzolan whose name originates from the city of Puzzuoli, near Napoli (Mt Vesuvio). According to Vitruvius Book V, 12, the traditional pozzolan was exclusively used for making piers into the sea or foundations for bridges, whereas harena fossicia, carbunculus and testa produced the concrete for buildings on land.
Roman concrete technology was more efficient than traditional building with hewn stone. The Table compares the construction time for the domes of most famous world monuments.
Monument | Dome Diameter | Date | Time | Material |
---|---|---|---|---|
Pantheon Rome | 43.30 m. | 118-125 AD | 7 years | concrete |
Ste-Sophia Istanbul | 32.60 m. | 532-567 AD | 5 years | concrete |
St.-Peter Rome | 42 m. | 1400-1564 AD | 50 years | stone |
Cathedral Florence | 42.20m. | 1420-1434 AD | 14 years | stone |
St.-Paul London | 30.80 m. | 1675-1710 AD | 35 years | stone |
Pantheon Paris | 21 m. | 1755-1792 AD | 37 years | stone |
Chemistry alone, however, will not make good concrete. The ancients mixed their cement, (cement, ash, and rock) with as little water as possible to give a stiff, “no-slump” concrete; and spread it on their cisterns and walls. After this it was pounded in the rock layer. Vitruvius, the noted Roman architect (20 BC) mentioned this process in his history of architecture. He also mentioned that special tamping tools were used to build a cistern wall.
This tamping process was very important. The close packing of the molecular structure by tamping reduced the need of excess water, which is a source of voids and weakness. Also close packing produces more bonding gel than might be normally expected.
Change in Roman Architecture Using this new technology, building could now be accomplished more rapidly and economically, and a great change took place in architecture. Cement could be formed within and over timber frameworks and so be used for such difficult construction as vaulting. The facing of cement walls usually consisted of smooth, irregularly shaped stones (opus incertum), of squared stones set on edge to form a neat network pattern (opus reticulatum, shortly after 100 BC), or of baked bricks (opus testaceum, from c.30 BC). These facings frequently provided the base for stucco or marble incrustation. Complex sequences of interior spaces with increasingly daring vaults and domes were constructed in the 1st and 2d centuries in baths, market buildings, and palaces; more and more of the traditional building types, such as temples and basilicas, were reshaped under the influence of the cement vault. The best-preserved example is the Hadrianic Pantheon (c.118-28; Rome), the temple to all the gods, with its huge, coffered-concrete dome spanning 43.3 m (142 ft).
The conventional forms of Etruscan and Greek architecture still continued to be used for many purposes. Originally prevalent in temples until the later Republic, the Tuscan order began to absorb some elements of the Greek Doric order and became Roman Doric.
The Greek Ionic order, and more so the Corinthian order, was widely used in Italy from the 2d century BC on. Probably in Augustan times elements of the Ionic and Corinthian capitals were fused.
A late-Republican development destined to have great success was the framing of the round arch with a superposed and generally engaged order, as on the outside of the colosseum (AD 72-82). With the ever-increasing use of concrete in the structure of buildings, the orders, originally structural, were gradually relegated to a purely decorative function.
Local materials, techniques, and building forms more or less dominated architecture in the provinces. The eastern Mediterranean continued in the established local and Greek Hellenistic building conventions, but imperial Rome succeeded in exporting to the East such building types as monumental baths, aqueducts, and, to some extent, amphitheaters, not previously found there.
Types of Civic Buildings In the early Republic the temple was still basically Etruscan–top-heavy with wide eaves and bulky terra-cotta decorations. In the 2d century BC, however, local traditions and Greek forms merged to create a more graceful structure: the podium and deep front porch of the Etruscan temple were retained and Greek proportions and forms adopted. This type of temple, generally employing the Corinthian order, gained ground rapidly in Italy and the West.
The Basilica, a multipurpose rectangular hall that may have originated in Greece, first appeared in Rome in the 2d century BC. Usually situated in the town forum, it generally had a spacious and lofty central hall covered with a flat ceiling and surrounded on all sides by a single- or double-colonnaded aisle, usually with a gallery.
The monumental honorary or triumphial arch began its history about 200 BC but received its standard form in the early Empire. Supported by stout piers, a centrally vaulted passageway carried an upper story, the attica, on which gilded bronze statues were placed. An engaged or partially freestanding order framed the piers and passage. Some arches had smaller passageways flanking the central vault. Contrary to Greek practice, the stage and semicircular orchestra and seating arrangement (cavea) were joined in the Roman theater to form one structure, often built on level ground with the cavea resting on a complex of vaulted substructures that doubled as access passageways. An intricately articulated columnar facade provided an elegant backdrop for the low stage. Similar substructures were built for the seating areas of the oval amphitheater, as in the Colosseum, and in the hairpin-shaped circus used for chariot races.
As early as 19 BC (Baths of Agrippa, Rome), huge, symmetrically planned imperial baths (thermae), which had large, sunken tubs and pools for crowds of people, were constructed. Some idea of the enormous, ingeniously vaulted halls can be seen today in the ruins of the Baths of Caracalla (AD 212-16; Rome; see Baths of Caracalla) and in the central hall of the Baths of Diocletian, (AD c.298-305 or 306, Rome; see Baths of Diocltian), which is now the church of Santa Maria degli Angeli. In an official register of AD 354, no fewer than 952 baths were listed in the city of Rome.
Roman Guilds One of the Roman’s secrets of success was their use of guilds. Almost all Roman builders came from guilds, each with their own name, such as the citrarii, or carpenters. Within the guilds, knowledge of materials, techniques and tools was kept and passed down from generation to generation. On top of this there were Roman building contractors who coordinated the various guilds in the construction of the buildings.
Along with this, the guilds, such as carpenters, stone masons, and metal workers were trained to make the Roman Legions self-supporting. Standards were introduced into the Legion for control, and with these, the Legion built military and civilian roads, fortifications, bridges, and other needed products. Before the soldiers retired from active service, their craftsmanship was transferred to their successors and to workers from local communities. In this way, the Legion was more than simply a fighting unit. It was also a construction and engineering unit.
Further History The secret of Roman success in making cement was traced to the mixing of slaked lime with pozzolana, a volcanic ash from Mount Vesuvius. This process produced a cement capable of hardening under water. During the Middle Ages this art was lost and it was not until the scientific spirit of inquiry revived that we rediscovered the secret of hydraulic cement – cement that will harden under water.
Excavations in Northampton, England, revealed three Saxon concrete mixers dating from about the year 700 AD. Labor to mix the concrete was supplied by either humans or animals. The concrete mixed at this time was inferior to the Roman concrete.
The Normans (1066) brought more sophisticated concrete technology to Britain when they landed in 1066. Reding Abbey in Berkshire, England, was built in 1130 by the Normans and still stands today. Concrete was also widely used in castles in England, including the White Tower in the Tower of London.
Repeated structural failure of the Eddystone Lighthouse off the coast of Cornwall, England, led John Smeaton, a British engineer, to conduct experiments with mortars in both fresh and salt water. In 1756, these tests led to the discovery that cement made from limestone containing a considerable proportion of clay would harden under water.
Making use of this discovery, he rebuilt the Eddystone Lighthouse in 1759. It stood for 126 years before replacement was necessary.
Other men experimenting in the field of cement during the period from 1756 to 1830 include L. J. Vicat and Lesage in France and Joseph Parker and James Frost in England.
The Reverend James Parker of Northfleet, England, patented what he called Roman cement in 1796. Its first major use was in mortar for a tunnel under the Thames River, which is still in use today, carrying trains between Whitechapel and New Cross.
Joseph Aspdin, and English mason, received a patent for modern, portland cement in 1824. He called it ‘portland’ because it produced a concrete similar in color to the limestone mined on the Isle of Portland, a peninsula in the English Channel. The first portland cement made in the U.S. was manufactured in 1871 at a plant in Coplaly, Pennsylvania.
In 1824, Joseph Aspdin, a bricklayer and mason in Leeds, England, took out a patent on a hydraulic cement that he called portland cement because its color resembled the stone quarried on the Isle of Portland off the British coast. Aspdin’s method involved the careful proportioning of limestone and clay, pulverizing them, and burning the mixture into clinker, which was then ground into finished cement.
Portland cement today, as in Aspdin’s day, is a predetermined and carefully proportioned chemical combination of calcium, silicon, iron, and aluminum. Natural cement gave way to portland cement, which is a predictable, known product of consistently high quality.
Before portland cement was discovered and for some years after its discovery, large quantities of natural cement were used. Natural cement was produced by burning a naturally occurring mixture of lime and clay. Because the ingredients of natural cement were mixed by nature, its properties varied as widely as the natural resources from which it was made.
Today, about 98 percent of the cement produced in the United States is portland cement. In Aspdin’s day, however, this new product caught on slowly. Aspdin established a plant in Wakefield to manufacture portland cement, some of which was used in 1828 in the construction of the Thames River Tunnel.
But it was almost 20 years later when J. D. White and Sons set up a prosperous factory in Kent that the portland cement industry saw its greatest period of early expansion, not only in England, but also in Belgium and Germany. Portland cement was used to build the London sewer system in 1859-1867.
The first recorded shipment of portland cement to the United States was in 1868, when European manufacturers began shipping cement as ballast in tramp steamers at very low freight rates. The volume increased to a peak of nearly 3 million barrels in 1885. After that date, Americans began producing increasing amounts of portland cement for themselves.
Nabataean Cement
As long ago as 50 BC Diodorus Siculus wrote in his book Bibliotheca Historica about the Nabataeans, “They are conspicuously lovers of freedom and flee into the desert, using this as a stronghold. They fill cisterns and caves with rainwater, making them flush with the rest of the land. They leave signals there which are known to themselves and not understood by anyone else. They water their herds every third day, so that they do not constantly need water in waterless regions, if they have to flee.” The information that Diodorus gathered was already common knowledge in the Middle East. The Nabataeans had been building hidden water cisterns for years.
As with the Romans, the Nabataeans secret to waterproof cement was the material known as pozzolan. Where the Romans used volcanic ash to create their waterproof cement, the Nabataeans had a much easier source. In the Hisma desert near Wadi Rumm are major surface deposits of silica, which geologists today claim is nearly 100% silicone.
B. Mason, in his book Principles of Geochemistry provides a technical discussion of research into geology to explain rock composition. For instance, he explains how a pozzolan material can be created by ground water seeping through silica. While the Romans had to search for this key component of ancient waterproof concrete, the Nabataeans simply had to locate places where water had seeped through the silica and scoop it up and add it to their lime plaster. (B. Mason, Principles of Geochemistry. John Wiley and Sons, New York, 1966, p. 160)
Another scientist, Dr. D. Orchard experimented with concrete and discovered that where crystalline silica was ground up very finely, it reacted with calcium. This is counter to the theory that only pozzolan materials react with calcium in making ancient concrete. It is interesting to note that some of the silica sand in the Hishma desert is so fine, that it is almost a white powder. (D. F. Orchard, Concrete Technology. Applied Science Publishers, London, 1973, p. 112)
The next issue that needs to be addressed is that of making lime. As I have traveled around the various Nabataean sites in the south of Jordan, I have noted a number of ancient lime pits. These pits were used for heating limestone to produce lime, and in some of the pits, large pieces of residue lime are still left.
Right: An ancient lime pit outside of the Grayn fort, located near Ras al Naqab in Southern Jordan
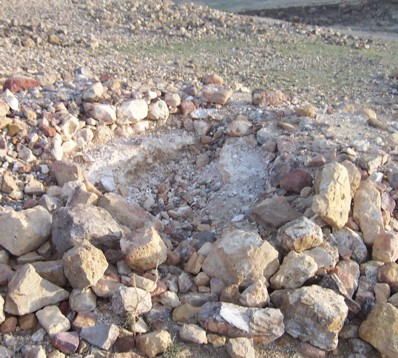
Lime making pit near Grayn in southern Jordan
While some historians believed that very high temperatures were needed to create lime, Green discusses in his book on pottery, the temperatures used to bake pottery. It turns out that the temperature for baking clay pots (used in a broken state to make concrete in Rome) is in the same range as the temperature used to drive the gases out of limestone in making lime - so the same kiln can be used in both cases. Temperature activates the pozzolan characteristic of the clay as found by the US Bureau of Reclamation. (D. Green, Pottery Glazes. Watson-Guptill Publisher, New York, 1973, p. 25.)
By applying fine silica sand to lime the Nabataeans could easily create waterproof cement. Lime was easily made, either in special lime pits, or in pottery kilns. The mortar that this combination produced would not only harden sufficiently to be waterproof, it would, in the right circumstances, harden, even under water. If the Nabataeans pounded the cement against the rocks, enough water would be pressed out of the cement to make it completely solid, and thus not only waterproof but also very strong and durable.
Today it is possible to observe evenly etched lines on the sides of Nabataean water cisterns, and even many of their buildings. In some locations, it is possible to see and test the very hard cement coating that covered the etched surface.
Thus, the Nabataeans had at their disposal all the elements to make waterproof cement. At present it is virtually impossible to tell when they developed this technique, although almost every Nabataean water cistern in existence had a coating of this substance. If the inference in the old Assyrian records is correct, and the Nabataeans were moving camel caravans in the Arabian desert as early as 700 BC, then it is possible to assume that they had developed the ability to make waterproof cement at this early date, as many of the ancient camel caravan routes would have required watering places in the desert between the major stopping places.
If this is the case, then the Nabataean’s ability to make waterproof cement was instrumental in their emerging as a distinct society, overcoming the obstacles of desert life and rising to the place of an empire.
Timeline of the Development of Cement Cement has been around for at least 12 million years. When the earth itself was undergoing intense geologic changes natural, cement was being created. It was this natural cement that humans first put to use. Eventually, they discovered how to make cement from other materials.
12,000,000 BC
Reactions between limestone and oil shale during spontaneous combustion occurred in Israel to form a natural deposit of cement compounds. The deposits were characterized by Israeli geologists in the 1960’s and 70’s.
3000 BC
Egyptians used mud mixed with straw to bind dried bricks. They also used gypsum mortars and mortars of lime in the pyramids. Chinese used cement like materials to hold bamboo together in their boats and in the Great Wall.
800 BC
Greeks, Crete & Cyprus used lime mortars which were much harder than later Roman mortars. The Nabataeans possibly made waterproof cisterns in the Arabian deserts during this time.
300 BC
Babylonians & as Syrians used bitumen to bind stones and bricks.
300 BC
Nabataeans undoubtedly built countless cisterns with waterproof cement by this date in Arabia. Many of these cisterns are still intact and continue to be used today.
200 BC - 476 AD
Romans used pozzolana cement from Pozzuoli, Italy near Mt. Vesuvius to build the Appian Way, Roman baths, the Coliseum and Pantheon in Rome, and the Pont du Gard aqueduct in south France. They used lime as a cementitious material. Pliny reported a mortar mixture of 1 part lime to 4 parts sand. Vitruvius reported a 2 parts pozzolana to 1 part lime. Animal fat, milk, and blood were used as admixtures (substances added to cement to increase the properties.) These structures still exist today.
500 - 1500 The Middle Ages
The quality of cementing materials in europe deteriorated. The use of burning lime and pozzolan (admixture) was lost, but reintroduced in the 1300’s.
1678
Joseph Moxon wrote about a hidden fire in heated lime that appears upon the addition of water.
1779
Bry Higgins was issued a patent for hydraulic cement (stucco) for exterior plastering use.
1780
Bry Higgins published “Experiments and Observations Made With the View of Improving the Art of Composing and Applying Calcereous Cements and of Preparing Quicklime.”
1793
John Smeaton found that the calcination of limestone containing clay gave a lime which hardened under water (hydraulic lime). He used hydraulic lime to rebuild Eddystone Lighthouse in Cornwall, England which he had been commissioned to build in 1756, but had to first invent a material that would not be affected by water. He wrote a book about his work.
1796
James Parker from England patented a natural hydraulic cement by calcining nodules of impure limestone containing clay, called Parker’s Cement or Roman Cement.
1802
In France, a similar Roman Cement process was used.
1810
Edgar Dobbs received a patent for hydraulic mortars, stucco, and plaster, although they were of poor quality due to lack of kiln precautions.
1812 -1813
Louis Vicat of France prepared artificial hydraulic lime by calcining synthetic mixtures of limestone and clay.
1818
Maurice St. Leger was issued patents for hydraulic cement. Natural Cement was produced in the USA. Natural cement is limestone that naturally has the appropriate amounts of clay to make the same type of concrete as John Smeaton discovered.
1820 - 1821
John Tickell and Abraham Chambers were issued more hydraulic cement patents.
1822
James Frost of England prepared artificial hydraulic lime like Vicat’s and called it British Cement.
1824
Joseph Aspdin of England invented portland cement by burning finely ground chalk with finely divided clay in a lime kiln until carbon dioxide was driven off. The sintered product was then ground and he called it portland cement named after the high quality building stones quarried at Portland, England.
1828
I. K. Brunel is credited with the first engineering application of portland cement, which was used to fill a breach in the Thames Tunnel.
1830
The first production of lime and hydraulic cement took place in Canada.
1836
The first systematic tests of tensile and compressive strength took place in Germany.
1843
J. M. Mauder, Son & Co. were licensed to produce patented portland cement.
1845
Isaac Johnson claims to have burned the raw materials of portland cement to clinkering temperatures.
1849
Pettenkofer & Fuches performed the first accurate chemical analysis of portland cement.
1860
The beginning of the era of portland cements of modern composition.
1862
Blake Stonebreaker of England introduced the jaw breakers to crush clinkers.
1867
Joseph Monier of France reinforced William Wand’s (USA) flowerpots with wire ushering in the idea of iron reinforcing bars (re-bar).
1871
David Saylor was issued the first American patent for portland cement. He showed the importance of true clinkering.
1880
J. Grant of England show the importance of using the hardest and densest portions of the clinker. Key ingredients were being chemically analyzed.
1886
The first rotary kiln was introduced in England to replace the vertical shaft kilns.
1887
Henri Le Chatelier of France established oxide ratios to prepare the proper amount of lime to produce portland cement. He named the components: Alite (tricalcium silicate), Belite (dicalcium silicate), and Celite tetracalcium aluminoferrite). He proposed that hardening is caused by the formation of crystalline products of the reaction between cement and water.
1889
The first concrete reinforced bridge is built.
1890
The addition of gypsum when grinding clinker to act as a retardant to the setting of concrete was introduced in the USA. Vertical shaft kilns were replaced with rotary kilns and ball mills were used for grinding cement.
1891
George Bartholomew placed the first concrete street in the USA in Bellefontaine, OH which still exists today.
1893
William Michaelis claimed that hydrated metasilicates form a gelatinous mass (gel) that dehydrates over time to harden.
1900
Basic cement tests were standardized.
1903
The first concrete high rise was built in Cincinnati, OH.
1908
Thomas Edison built cheap, cozy concrete houses in Union, NJ.
1909
Thomas Edison was issued a patent for rotary kilns.
1929
Dr. Linus Pauling of the USA formulated a set of principles for the structures of complex silicates.
1930
Air entraining agents were introduced to improve concrete’s resistance to freeze/thaw damage.
1936
The first major concrete dams, Hoover Dam and Grand Coulee Dam, were built. They still exist today!
1967
First concrete domed sport structure, the Assembly Hall, was constructed at The University of Illinois, at Urbana-Champaign.
1970’s
Fiber reinforcement in concrete was introduced.
1975
CN Tower in Toronto, Canada, the tallest slip-form building, was constructed. Water Tower Place in Chicago, Illinois, the tallest building was constructed.
1980’s
Superplasticizers were introduced as admixtures.
1985
Silica fume was introduced as a pozzolanic additive. The “highest strength” concrete was used in building the Union Plaza constructed in Seattle, Washington.
1992
The tallest reinforced concrete building in the world was constructed at 311 S. Wacker Dr., Chicago, Illinois.
Bibliography and books on cement and related issues.
Adam, J. P., La Construction Romaine. Grand Manuels Picard, Paris, 1984, p.86-87.
Azaroff, L. V., Introduction to Solids. McGraw Hill Book Co., New York, 1960, p. 431
Azbe, V.J., Theory and Practice of Lime Manufacture. Rock Products Publisher, 1946, p. 129.
Bailey, C., The Legacy of Rome. Clareton Press, Oxford, 1968, p. 439
Bailey, K. C., Plinus Secundus-The Elder Pliny. Arnold Publisher, London, 1929, p. 145.
Balsdon, J. P. V. D., The Romans. Basic Books, Inc., New York, 1965, p. 183.
Banks R. F., and M. L. Kennedy, The Technology of Cement and Concrete. John Wiley & Sons, New York, 1955, p. 16.
Barraclough, G., The Times Atlas of the World History. Times Books Ltd., London, 1983, p. 273
Blake, M. E., Ancient Roman Construction in Italy from the Prehistoric Period to Augustus. Carnegie Institute of Washington, Washington, D.C., #570, 1947, p. 322.
Blake, M. E., Construction in Italy from Tiberius through the Flavians. Carnegie Institute, Washington, D.C., 1959, p. 161.
Braidwood R. J., and G. R. Willey, Courses Toward Urban Life. Adline Publishing, Chicago, 1962, p. 73
Branda F., Luciani, G, Costantini A, Piccioli C, Interpretation of the Thermogravimetric curves of Ancient Prozzolanic Concretes, Archaeometry, Volume 43, Part 4, November 2001
Brownell, W. E., Structural Clay Products. Springer-Verlag Publisher, N.Y., 1976, n. 2
Buchan, J., Augustus. Hodder and Stoughton, St. Paul’s House, London, 1947, p. 255
Bye, G. C., Portland Cement Composition Production and Properties. Pergamon Press, Oxford, 1983, p. 111
Carcopino, J., Daily Life in Ancient Rome. Yale University Press, New Haven, N.J., 1969, p. 63
Charlesworth, M. D., The Roman Empire. Oxford University Press, Oxford, 1968, p. 27
Chesters, J. M., Refractories: Production and Properties. The Iron and Steel Institute, London, 1973, p. 69.
Chevallier, R., Roman Roads. University of California Press, Berkeley, 1976, p. 83
China, T., Building Industry. Pride of the Pacific. Honolulu, Hawaii, July 1991, p. 22
Conophogos C. and H. Badeca, The Water Cisterns of Ore Washers in Laurion and Their Special Hydraulic Mortar. Athens University of Geology Publisher, 1975, p. 336
Cowan, H. W., The Master Builders. John Wiley and Son, New York, 1977, p. 73
Daumas, M., A History of Technology and Invention. Crown Publishers, New York, 1969, p. 246
Davidovits, Joseph, Emeritus Professor, Geopolymer Institute, http://www.geopolymer.org,
de Camp, L. S., The Ancient Engineers. Dorset Press, New York, 1990, p. 195
Deer, W. A., Rock-forming Minerals. Longmans, London, 1967, p. 213.
Dudley, D. R., The Romans: 850 B.C.-A.D. 337. Alfred A. Knopf, New York, 1970, p. 170.
Eckel, E. C., Cements, Limes, and Plasters. John Wiley & Sons, New York, 1922, p. 576.
Eglinton, M. S., Concrete and Its Chemical Behavior. Thomas Telford, London, 1987, p. 6.
Eichholz, D. E., Pliny: Natural History. Harvard University Press, Cambridge, Mass., 1962, p. 147
Finley, M. I., The Ancient Economy. University of California Press, Berkeley, 1974, p. 176
Fink, R. O., Roman Military Records on Papyrus. American Philogical Association, William Clowes and Sons, London, 1971, p. 196
Fitchen, J., Building Construction Before Mechanization. MIT Press, London, 1988, p. 143
Fletcher B., and R. A. Cordingley, A History of Architecture. Charles Scribner & Son, New York, 1967, p. 177.
Forbes, R. J., Antiquity. E. J. Brill Publisher, Leiden, 1950, p. 132.
Forbes, R. J., Man the Maker. Abelard Schuman Ltd., London, 1958, p. 72
Fowler, W. W. Social Life at Rome. Macmillan Co., London, 1965, p. 31
Gest, A. P., Engineering. Copper Square Publisher, Inc., New York, 1963, p. 40.
Ghosh S. N., and A. K. Chatterjee, Advances in Cement Technology. Pergamon Press, N.Y., 1983, p. 538
Gibbon, E. The Decline and Fall of the Roman Empire. Harcourt, Brace and Company, New York, 1960, p. 891.
Gibson, Dan, The Nabataeans, Builders of Petra, CanBooks, Amman, Jordan, 2002
Ginouves R., and R. Martin, Dictionary of the Methods of Greek and Roman Architecture. University of Paris at Paris, Vol. 1, 1985, 130
Grant, M., The Army of Caesars. Charles Scribner’s Sons, New York, 1973, p. 33.
Grant, M., The World of Rome. The World Publishing Co., New York, 1960, p. 109.
Green, D., Pottery Glazes. Watson-Guptill Publisher, New York, 1973, p. 25.
Hadas, M., Imperial Rome. Time-Life Books, Alexandria, Virginia, 1975, p. 82.
Hamey, L. A. and J. A., The Roman Engineers. Cambridge University, Cambridge, 1981, p. 42
Hamlin, T., Architecture Through the Ages. G. P. Putnam’s Sons, New York, 1953, p. 161
Heichelheim F. M., and C. A. Yeo, A History of the Roman People. Prentice-Hall, Inc., Englewood Cliffs, N.J., 1962, p. 412
Hodges, H., Technology of the Ancient World. Alfred A. Knopf, New York, 1970, p. 184
Jenkin, C. F., An Inaugural Lecture of the Training of the Engineering Profession. University of Oxford Press, 1908, p. 12
Johnston, H. W., The Private Life of the Romans. Cooper Square Publishers, Inc., New York, 1973, p. 172
Jones, A. H. M., Augustus. W. W. Norton Co., New York, 1970, p. 10.
Jones, A. H. M., The Later Roman Empire: 284-602 AD, Vol. II. University of Oklahoma Press, Norman, OK, 1964, p. 1013.
King, A., Archaeology of the Roman Empire. Bison Books Ltd., London, 1988, p. 10
Kingery, W. D., Ancient Technology to Modern Science, Vol. I. The American Ceramic Society Publisher, Columbus, Ohio, 1985, p. 20.
Knibbs, K. V. S., The Chemistry, Manufacture and Use of the Oxides, Hydroxides, and Carbonates of Calcium and Magnesium. Earnest Benn Ltd. Publisher, London, 1924, p. 4.
Komendant, A. E., Contemporary Concrete Structures. McGraw-Hill Book Co., New York, 1972, p. 352.
Lanciani, R., The Ruins and Excavations of Ancient Rome. Benjamin Bloom Publisher, New York, 1967, p. 561
Lea, F. M., The Chemistry of Cement and Concrete. St. Martin Press, New York, 1956, p. 367
Levi, D., The Italian Excavations in Crete and the Earliest European Civilization. Italian Institute of Culture Publisher, Dublin, 1963, p. 6.
Licht, K. D., The Rotunda in Rome. Jutland Archeological Society Publisher, Copenhagen, 1968, p. 92.
Lugli, G., The Pantheon and Adjacent Structures. Giovanni Bardi Publisher Rome, 1971, p. 20.
Nash, E., Pictorial Dictionary of Ancient Rome, Vol. I. Frederick A. Praeger, New York, 1968, p. 38 and 46.
Macaulay, D., City-A Story of Roman Planning and Construction. Houghton Miffin Company, Boston, 1974, p. 28.
MacDonald, W. L., The Architecture of the Roman Empire. Yale University Press, London, 1965, p. 158.
MacDonald, W. L., The Pantheon. Harvard University Press, Cambridge, Mass., 1976, p. 37.
MacMullen, R., Soldier and Civilian in the Later Roman Empire. Harvard University Press, Cambridge, Mass., 1967, p. 173
Malinowski, R., Concrete and Mortars in Ancient Aqueducts. Concrete International: Design and Construction. Detroit, Michigan, Jan. 1979, p. 75
Maloney J., and B. Hobley, Roman Urban Defences in the West, Report 51. Council for British Archaeology Pub., 1983, p. 26
Mark R., and P. Hutchinson, On the Structure of the Pantheon, Art Bulletin. March 1986, p. 29
Mason, B., Principles of Geochemistry. John Wiley and Sons, New York, 1966, p. 160.
Mason, O. T., The Origins of Invention. The MIT Press, Cambridge, Mass., 1966, p. 111.
Mercer, H. C., Ancient Carpenters Tools. The Bucks County Historical Society, Doylestown, Penn., 1960, preface
Middleton, J. H., The Remains of Ancient Rome. Adam and Charles Black Publishers, London, 1892, p. 47
Mielenz, R. C., Concrete as a Modern Material, Modern Materials. Academic Press, New York, 1965, p. 276.
Mielenz, R. C. Effect of Calcination on Natural Pozzolan, Symposium on Use of Pozzolanic Materials in Mortars and Concrete, Publication #99. American Society of Testing Materials, “ Philadelphia, PA”, 1950, P. 52.
Moore, David, The Riddle of Ancient Roman Concrete, Internet, 1999
Moore, David, The Roman Pantheon: The Triumph of Concrete, 1999
Morgan, M.H., Vitruvius - The Ten Books on Architecture. Dover Publications, New York, 1960, p. 248
Neuburger, A., The Technical Arts and Science of the Ancients. Macmillan Co. New York, 1930, p. 408.
Orchard, D. F., Concrete Technology. Applied Science Publishers, London, 1973, p. 112.
Orlandos, A. K., Les Materiaux de Construction. Editions E. de Boccard, Paris, 1966, p. 139.
Patton, W. M., A Treatise on Civil Engineering. John Wiley and Son, N.Y., 1905, p. 175.
Peckworth, H. F., Concrete Pipe Handbook. American Concrete Pipe Assoc., Chicago, 1959, p. 12
Petrie, W. M. F., Tools and Weapons. British School of Archaeology in Egypt, Hazell, Watson, and Viney, London, 1917, p. 43.
Potter, T. W., Roman Italy. University of California Press, Berkeley, California, 1990, p. 141
Popovics, S., Concrete-Making Materials. McGraw-Hill Book Co., New York, 1979, p. 77.
Ramachandran, V. S., Applications of Differential Thermal Analysis in Cement Chemistry. Chemical Publishing Co., New York, 1969, p. 214
Rehaut, E. B., Cato the Censor on Farming. Octagon Books, Inc., New York, 966, p. 64.
Robertson, D. S., Greek and Roman Architecture. At the University Press, Cambridge, 1971, p. 232.
Rowden, E., Firing of Brick. Thomas Forman And Son, Nottingham, England, 1973, p. 2
Sandy, J. E., A Companion to Latin Studies. Hafner Publishing Co., New York, 1968, p. 317
Scott R. F., and J. J. Schoustra, Soil Mechanics and Engineering. McGraw-Hill Book Co., New York, p. 283.
Singer, C., A History of Technology, Vol. III. At The Clarendon Press, Oxford, 1967, p. 448
Spier, R. F. G. From the Hand of Man. Houghton Mifflin Company, Boston, 1970, p. 35.
Strong D., and D. Brown, Roman Crafts. Gerald Duckworth Co. Publisher, London, 976, p. 212.
Symposium on Use of Pozzolanic Materials in Mortars and Concrete. Publication #99, ASTM, American Society of Testing Materials, Philadelphia, 1950, p. 51
Taylor, A., Metallography. John Wiley & Sons, 1949, New York, p. 302.
Taylor, H. F. W., The Chemistry of Cements. Academic Press, London, 1964, p. 70
Taylor, W. H., Concrete Technology and Practice. Angus and Robertson Publisher, 1965, p. 256
Van Deman, E. B., The Building of the Roman Aqueducts. Carnegie Institution of Washington, Washington, DC, 1934, p. 10 and 204
Van Vlack, L. H., Elements of Materials Science. Addison-Wesley Publishing Co., Reading, Mass., 1967, p. 386
Von Hagan, V. W., The Roads That Lead to Rome. The World Publishing Co., New York, 1967, p. 35
Waddell, J. J., Construction Materials Ready Reference Manual. McGrawHill Book Co., New York, 1985, p. 87.
Walker, D. S., Geography of Italy. Butler and Tanner, London, 1967, p. 173
Ward-Perkins, J. B., Roman Imperial Architecture. Penquin Books, New York, 1983, p. 472.
White, K. D., Greek and Roman Technology. Cornell University Press, Ithaca, New York, 1984, p. 205
Wilby, C. B., Concrete for Structural Engineers. Newnes Butterworths, London, 1977, p. 142
Williams, T. I., The History of Invention. Facts on File Publications, New York, 1981, p. 60
Winklemaw, B., Editor, The Times Atlas of World History. Hammond Pub., Maplewood, NJ, 1979, p. 91.
Woodforde, J., Bricks to Build a House. Routledge and Kegan Paul Publisher, London, 1976, p. 21, 26
Zumberge, J. H., Elements of Geology. John Wiley & Sons, New York, 1963, p. 32
Page Discussion
Membership is required to comment. Membership is free of charge and available to everyone over the age of 16. Just click SignUp, or make a comment below. You will need a user name and a password. The system will automatically send a code to your email address. It should arrive in a few minutes. Enter the code, and you are finished.
Members who post adverts or use inappropriate language or make disrespectful comments will have their membership removed and be barred from the site. By becoming a member you agree to our Terms of Use and our Privacy, Cookies & Ad Policies. Remember that we will never, under any circumstances, sell or give your email address or private information to anyone unless required by law. Please keep your comments on topic. Thanks!